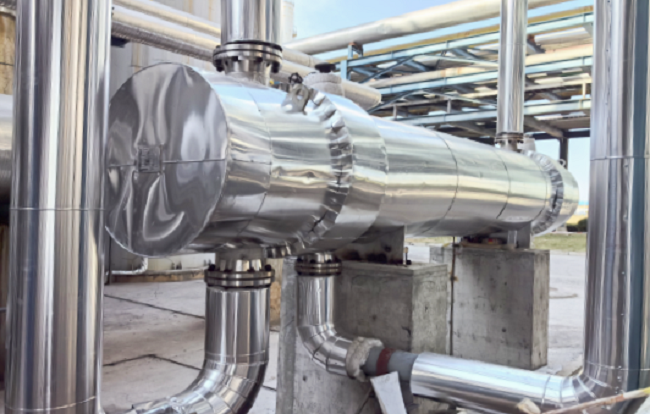
在晋能控股装备制造集团“五小”创新优秀成果评选中,华昱公司生产管理部凭借冷凝液余热高效回收项目斩获优秀奖。这一成果的背后,有一支长期“埋头”在生产现场,每天和生产数据“打交道”的管理人员、技术人员队伍,他们知道任何一点微小的变化,乘以百万吨都是一个庞大的数字。所以,哪怕只是动了一个小小的阀门,或者调整了一个小小的指标,都会触动他们的“神经”,于是,他们逐渐养成了一个工作习惯,每天下班前,都会把当天发现的可以优化的地方,记录在表格里,以便继续思考和计算。
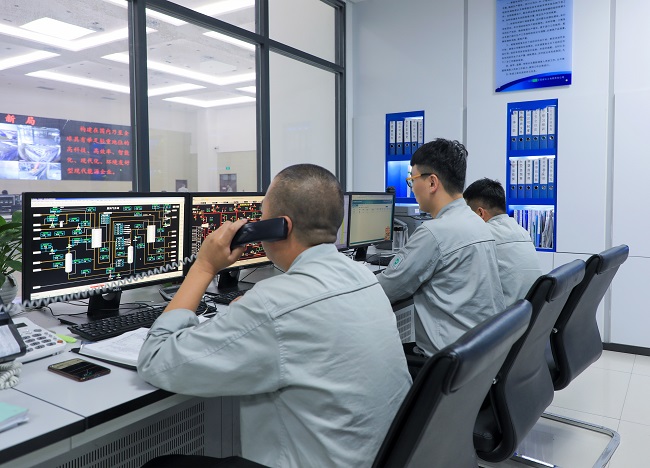
直面问题 探索节能路径
在生产过程中,空分2.5MPa蒸汽冷凝液和低温甲醇洗2.5MPa蒸汽冷凝液因原设计缺陷,在回收至蒸汽冷凝液管线时会出现严重液击现象,导致不得不暂时将其排入循环水池。然而,这些冷凝液温度高达150℃,直接排放不仅造成能源浪费,也与国家“双碳”政策背道而驰。为响应国家号召,降低用能总量,该公司启动了对ORC余热发电、溴化锂制冷冻水及冷凝液余热系统自循环利用三种余热回收方案的综合评估,力求找到最优解。
科学比选 锁定高效方案
该公司公关组经过对三种余热回收方式的深入研究,从投入成本、热回收效率及收益率三个维度进行对比分析。结果显示,冷凝液余热系统自循环利用凭借投入最低、能量回收率最高、经济性最强的优势脱颖而出。孙刚说:“我们通过进一步优化方案,分析现有生产系统热平衡网络,精准锁定热电冷渣机冷却脱盐水回水作为冷源,并针对冷凝液(150℃、29m³/h)与冷渣机冷却水(48℃、80m³/h)的参数差异,量身定制余热回收换热器”。
精准实施 投运效果显著
在变换装置中,该公司公关组通过新增一台蒸汽冷凝液余热回收换热器,实现了高温冷凝液与冷脱盐水的热能交换:热脱盐水吸收冷凝液余热后,温度从48℃升至76℃,送回除氧器;降温后的冷凝液(约100℃)并入0.5Mpa蒸汽冷凝液管网,最终进入脱盐水站水箱循环利用。项目投运后,除氧器蒸汽消耗量直降3.42吨/小时,年经济效益达187.8万元,设备运行稳定,完全达到预期目标。
此次改造的成功不仅解决了公司冷凝液回收的液击难题,更验证了冷凝液余热自循环系统的技术可行性与经济优势,其高投入产出比和高效能量回收能力还为同类企业提供了可借鉴的范例经验,尤其在化工、电力等行业中具有广阔的推广空间。